Call 1-800-223-0012
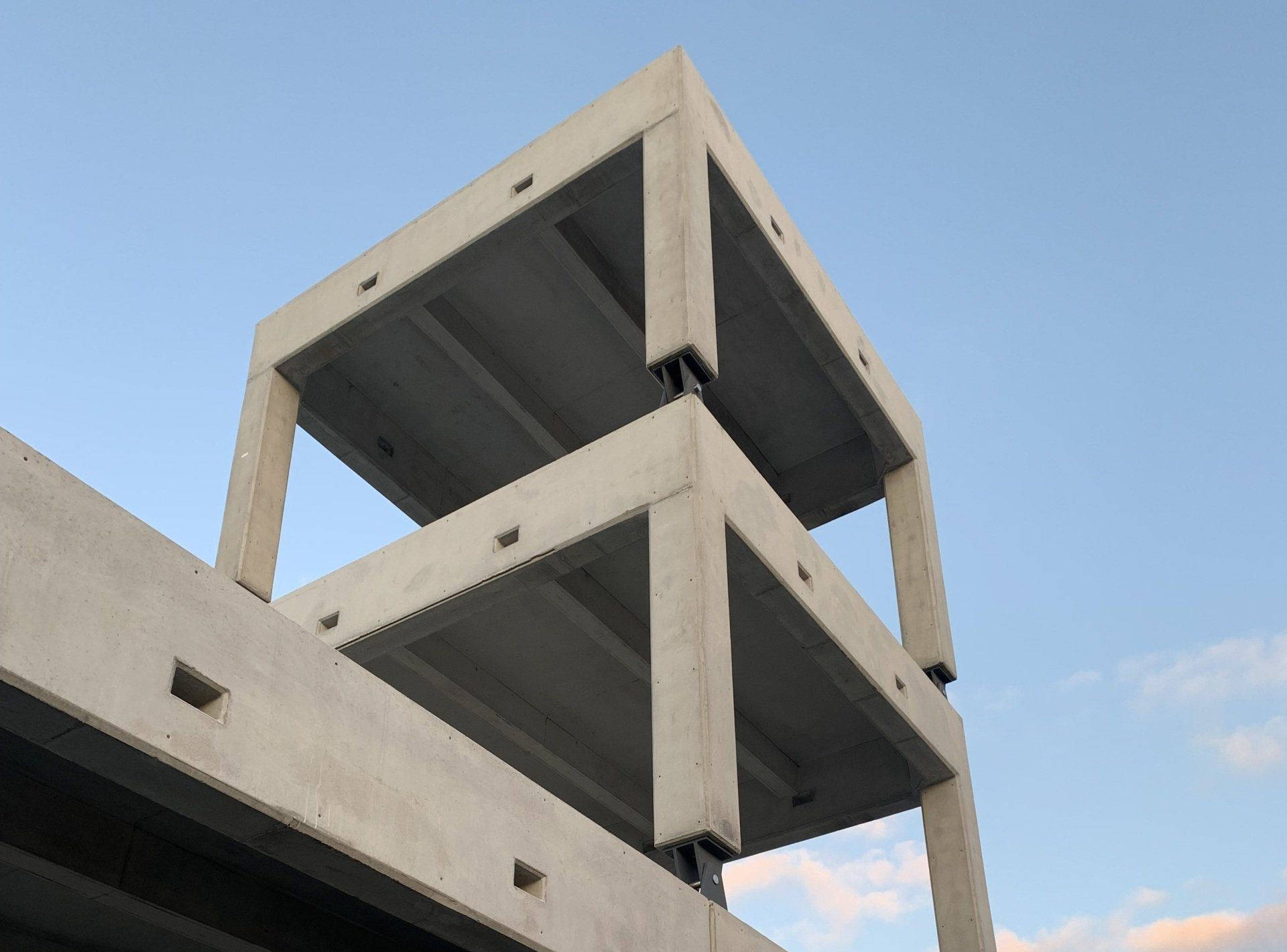
Benefits and Features of Lodestar Structures
Lodestar Modular Building Units (MBUs) allow you to complete more construction projects, on time and on budget. MBUs optimize the use of space, providing more usable interior and exterior space, including functional rooftop access.
Save time and money
Fast and Efficient Construction Planning
Save time, money and get more usable space with Lodestar framing when compared to traditional framing. Lodestar structures allow for fast and efficient construction planning and enable you to maximize interior and exterior spaces.
Traditional Framing
Traditional framing has the potential for misunderstanding floor plans, for construction errors and quality imperfections.
Higher demand for skilled labour workers means:
Lodestar Framing
Modular framing reduces the opportunity for floor plan errors. Quality and workmanship are managed in a climate-controlled factor.
Reduced demand for skilled labour workers means:
Space Optimization
Maximization of Interior and Exterior Spaces
Modular Building Units optimize the use of space and provide more usable interior and exterior space, including functional rooftop spaces.
Traditional Framing
Interior Main Level | 1,000 sq ft |
Interior Second Level | 846 sq ft |
Interior Total Usable Space | 1, 846 sq ft |
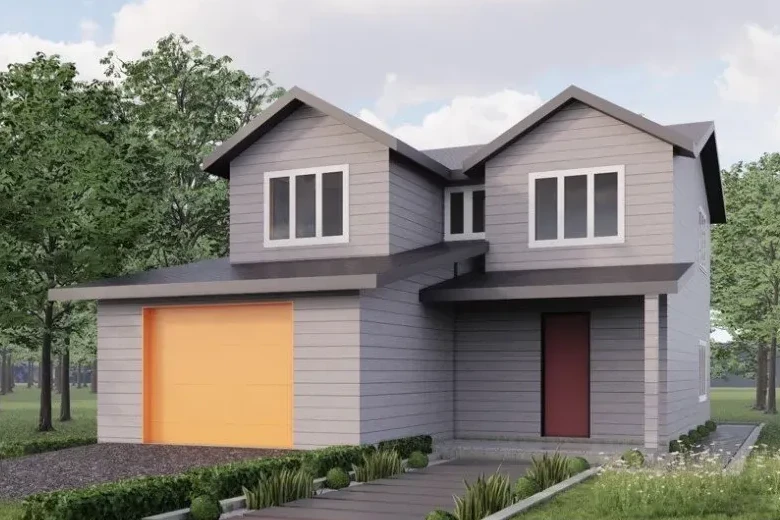
Ground Level Green Space | 2,131 sq ft |
Rooftop Level Green Space | 0 sq ft |
Total Usable Green Space | 2,131 sq ft |
Lodestar Framing
Interior Main Level | 1,000 sq ft |
Interior Second Level | 954 sq ft |
Interior Total Usable Space | 1, 954 sq ft |
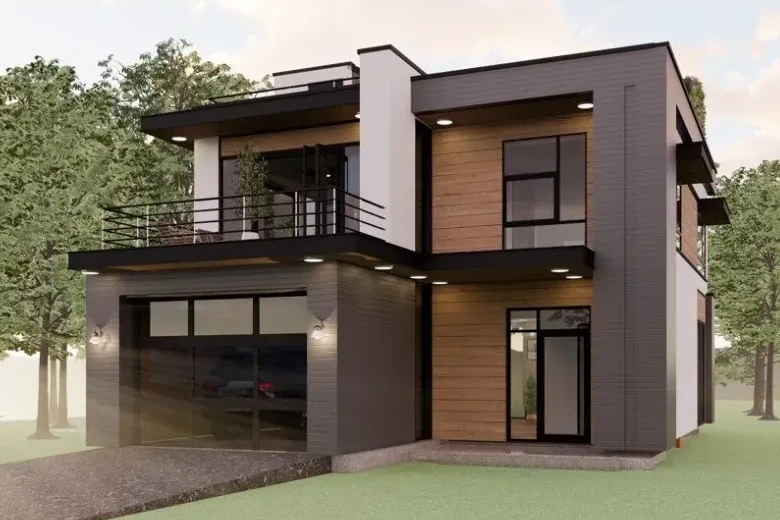
Ground Level Green Space | 2,131 sq ft |
Rooftop Level Green Space | 1,019 sq ft |
Total Usable Green Space | 3,150 sq ft |
Installation in a Fraction of the Time
More Projects in Less Time
A Lodestar structure provides the equivalent of the roof component, upper-level flooring, roof support pillars, wall support-framing, and the interior roof. The modules are designed to be installed in a fraction of the time it would take to complete the equivalent using traditional materials.
The inherent benefits of the design of the module include enhanced two-hour fire rating, structural resilience, natural climate control, and usable rooftop space, allowing for optimal use of interior and exterior space.
Increased cost control, and waste reduction, is achieved by reducing exposure to unforeseen weather or work-related delays. The result is an efficient and more manageable construction schedule, allowing more projects to be completed with less impact related to resource availability.
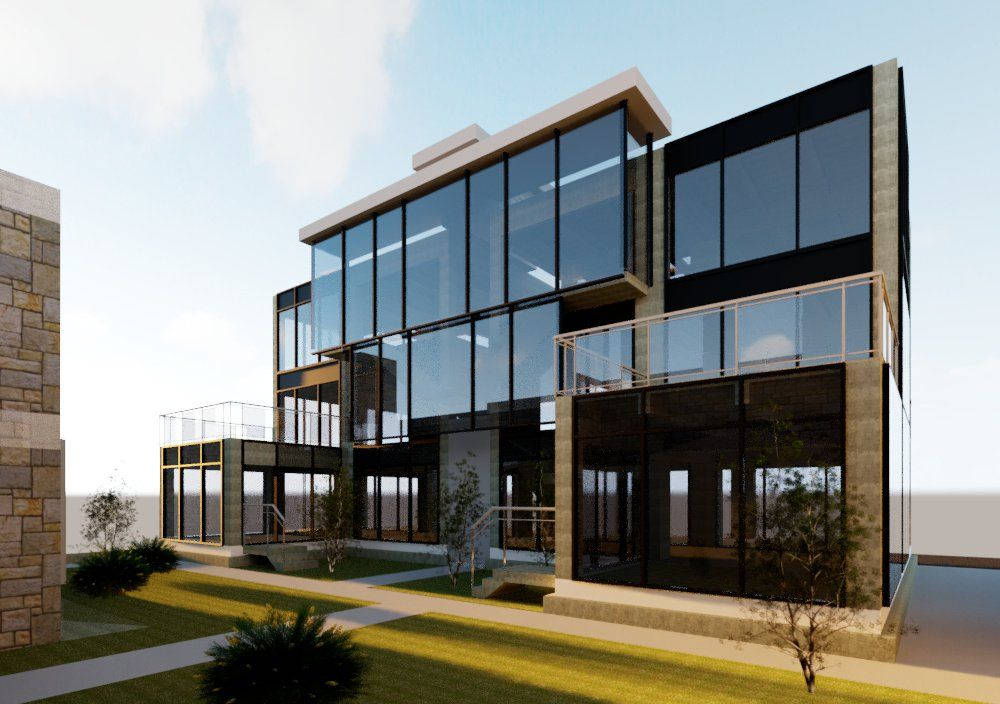
Benefits of Building with Lodestar
LODESTAR MBU’s provide designers and architects an extended platform to create unique and custom design options. MBU’s can be used as the infrastructure around which they can design traditional designs, or specific characteristics can remain exposed to achieve custom and unique features. LODESTAR MBU features can remain exposed to provide a transition from internal building features to external features of pools, driveways, retaining walls, etc.
LODESTAR MBU’s are prebuilt offsite and can be scheduled for delivery to construction sites as required. For large projects MBU’s can be staged at the construction site and used on demand, the identical modular nature allows the MBU’s to be deploying without the need to use specific modules. MBU’s can be rapidly placed into position, reducing the framing time by as much as 90%. Each MBU provides framing and roofing features, reducing additional steps, and allowing an accelerated enclosure and finishing schedule. Building with LODESTAR MBU’s can reduce construction projects by up to 50%.
LODESTAR MBU’s provide the primary framework of the building, reducing the need for most of the framing and roofing crews. Fewer subcontractors are needed in this type of construction, lowering labor costs, and increasing productivity with a smaller labor force. Combining modular building material further reduces the labour requirements while further expediting the construction process.
Operations, scheduling, and administration becomes more efficient using LODESTAR MBU’s. Building materials can be custom ordered in sizes and volumes, reducing the demand for onsite tasks, allowing project managers to concentrate on completing tasks quickly and with controlled complexity. LODESTAR MBU’s immediately provide protection from weather elements, providing the framework which allows construction teams to rapidly enclose the building and eliminate the risk of weather-related construction delays.
LODESTAR MBU’s reduce time-waste, material-waste, delay-waste, and resource-waste. MBU’s are prebuilt offsite in a factory where exact materials are calculated and used, they are delivered to the construction sites on schedule, and allow for an accelerated on-site construction process with reduced skilled labour and trades. The structural integrity of MBU’s allow architects to remove non-essential construction features such as trusses and traditional roofing. The efficiencies experienced in all aspects of the construction cycle allow the project to proceed on schedule, with reduced risk of unforeseen costs.
LODESTAR MBU’s are made of durable precast concrete, significantly reducing potential property damage and loss during disasters like storms, floods, and fire. Insurance premiums during construction may also be lower due to reduced fire damage and material theft. MBU’s are hoisted into place using cranes, reducing the need for workers to construct framing or roofing at dangerous heights, limiting exposure to insurance claims for workplace accidents. Concrete is less susceptible to moisture or water damage, which could result in structural damage or material rot, which would lead to costly insurance claims and likely increased insurance premiums.
The modular design allows for future expansion plans with ease and minimal costs. Modules can be added Horizontally and/or Vertically at the time of original construction or can be schedule for a future-dated expansion phase.
Benefits of Concrete
Concrete is the most-produced man-made material on Earth. Concrete’s durability, strength and cost effectiveness make it the optimum building material for infrastructure networks worldwide. Houses, schools, hospitals, recreational amenities, airports, bridges, highways, and rail systems have been made possible with the use of Concrete. The use of concrete in the construction process is steadily increasing to keep up with the demand for urban development, construction to withstand extreme weather events, and the price of other infrastructure materials continues to rise.
Concrete can be incorporated in several key aspects to make projects more durable and disaster resistant. For example, concrete wall, floor and roof systems offer an unsurpassed combination of structural strength and wind resistance. In addition, hardened exterior finishes for walls and roofs of a home or business provide the best combination of strength and security.
Building with concrete is cost effective due to the ability to have components produced under extreme quality-controlled processes, in climate-controlled conditions, and delivered to the construction site as a ready to be installed building component. Time and material savings, combined with the reduction in labor requirements, and less opportunities for unforeseen events, allows projects to be competed on time and withing budgetary expectations.
A concrete structure is a long term, quality-based building material, superior to most traditional wood or steel-framed structures. A concrete infrastructure can withstand water and moisture, infestation, fire, and extreme acts of nature such as tornadoes, hurricanes, and earthquakes.
Concrete structures are better able to resist damage from extreme weather, and generally last longer. Damage from major weather events is less severe and affected communities will spend less energy and fewer resources repairing their community, allowing them to quickly recover to a pre-disaster status.
Concrete retains surrounding temperatures for prolonged periods, moderating temperature fluctuations and minimizing temperature transfer between the exterior and the interior of a building. The concrete mass retains heat absorbed from sunshine, which is gradually released over the nighttime, and absorbs the cool during the evening which is gradually released during the daytime hours. This results in significantly reduced heating and cooling costs, provides a more consistent and comfortable environment, and allows the temperature to be managed by smaller and more efficient HVAC systems.
Concrete is durable and resilient, capable of withstanding weather extremes and required minimal maintenance or upkeep. The inherent resistance to erosion, rot, or insects, ensures buildings will be structurally secure for up to ten times the life expectancy of traditional building materials.
Building with concrete saves time, allowing builders to complete large sections in a shorter period, using forms, precast solutions, or pouring onsite. Each application provides its own time saving benefit and flexibility of use.
Concrete sets at a regular ambient or room temperature and can be used with minimal temperature management. Concrete can also be produced specifically to set in a variety of weather or climate variations. Modular building units can be manufactured in climate-controlled facilities where temperatures are regulated, and product schedules can be managed without climate related concern.
LODESTAR MBU’s make up the main infrastructure, around which the building is constructed, allowing architects and builders to utilize a wide variety of traditional and modern building materials to enclose and finish the construction. LODESTAR MBU’s are built to the highest quality standard including a smooth finished surface which, if desired can be left exposed as design characteristics otherwise not available with traditional building materials. LODESTAR MBU’S provide the best of both options, while adding multiple levels of design and structural integrity and durability.
Concrete is a common product used in most construction projects, can be matched with material used on external features of Pools, driveway, retaining walls, etc. Concrete can be stamped, molded, colored, finished, or enclosed with other material, to achieve desired design aesthetics. The structural integrity allows concrete to be used as both a structural material and a finishing material, suitable for use in most construction projects.
Concrete can be produced in the exact amount required for a specific job, eliminating the opportunity for excess product which is often attributed to waste. Concrete can also be recycled and used repeatedly in construction projects.
Concrete is produced to both last for an extended period, and with the flexibility to be converted multiple times, used for other purposes throughout its lifespan. When casted into Modular components it adds to the ability of re-use and repurposing the products.
Concrete dampens noise and reduces noise transfer than traditional materials, reducing noise from transferring from internal and external sources. The reduction of sound transfer results in quieter spaces and increased privacy.
Concrete can be produced locally, delivered to the construction site with reduced delivery and travel times. Delivery schedules can be coordinated to ensure the necessary volumes are delivered when and where required, further reducing delays and associated costs. Producing concrete locally ensures the material is produced to withstand the local climate conditions.
A prominent raw material in concrete is limestone, which is one of the most abundant resources on the planet. Concrete can also be produced with alternative materials including waste byproducts from steel mills and power plants.
Unlike wood or steel, concrete does not burn, soften, or bend, concrete structures are more likely to remain standing through a fire. As the infrastructure of the building, fire-resistance enhances safety and security during the construction process and the finished product. The structure’s fire rating satisfies a higher level of fire code requirements, allowing for a more versatile use of the structure in more industry sectors.
Moisture does not affect concrete to the degree it would wood or metal materials. Buildings built near waterfront or in areas at risk of flooding will have a much longer lifespan if they are constructed out of Concrete vs. wood or steel. Most buildings incorporate concrete into the design, often used for flooring, footings, or subterrain walls. Concrete is used due to its strength, durability, and resistance to environmental elements.
Benefits of Modular
Modular construction is a product built off-site, in a factory controlled environment, by highly skilled staff, applying calibrated equipment, using the same materials and designed to the same codes and standards a s conventionally built facilities – but in about half the time. Buildings are produced in “modules” that when put together on site, reflect the identical design intent and specifications of the most sophisticated site-built facility – without compromise.
LODESTAR MBU’s are manufactured in a climate-controlled facility and delivered to the construction site for immediate installation or can be staged at the location awaiting installation. This allows builders to schedule the delivery and installation in an efficient manner, in most cases the complete structure is erected in a one to two days.
The complexity of scheduling and managing multiple trades, equipment and supplies has the potential to result in unexpected costs, delays, and waste. LODESTAR MBU’s allow builders to easily manage the process and provides the ability to advance the building process to framed and enclosed in a very condensed period, reducing weather related delays, and with reduced demand for labor or supplies. The efficiencies prevent unexpected costs from occurring, keeping the project on budget.
LODESTAR MBU’s are manufactured in a climate-controlled facility and can be stored at a location awaiting installation. Production performed by dedicated highly skilled workers, under a controlled and monitored quality process, with assurance inspections at every step of production cycle. The completed units are put though a final multi-pion inspection before released from the production plant.
LODESTAR MBU’s provide a flat roof element which would allow builders to repurpose disrupted ground-level greenspace to the rooftop, eliminating the negative construction impact. LODESTAR MBU’s are manufactured in regionally located climate-controlled factories where waste is reduced from the process by skilled employees, material tolerances are optimized using the proper tools in a controlled environment, and delivery distances are minimalized.
The controlled manufacturing process provides assurance all products are manufactured under optimum temperature conditions, by highly trained and skilled workers, with automated mixture controls, and allowed to cure for a consistent period. Each step of the process is essential to ensure the finished product meets the highest quality control standards in the industry.
The factory-controlled process generates less waste, creates fewer site disturbances, and allows for tighter construction schedules.
A benefit of incorporating LODESTAR MBU’s into the construction process is that it reduces the amount and length of construction noise produced by traditional onsite construction, and once the structure is enclosed the noise is further reduced. Reducing the length and volume of noise pollution is essential when building in densely populated areas and in noise sensitive areas.
LODESTAR MBU’s are built offsite reducing the demand on scheduling skilled labor at the jobsite. Reduced labor translates into reduced risk of injury, labor accidents, and reduced demand for supervisory duties.
The regulated need for trades simplifies the responsibilities of the General contractor while reducing costs and construction delays.
The construction process advances quickly from footings to framed in structure, reducing the frequency of onsite inspections for construction, and building code compliance officials.
LODESTAR MBU’s are manufactured to align precisely to other MBU’s. The production process is completed by highly skilled workers, under a controlled and monitored quality process, with assurance inspections at every step of production cycle.
Precast molds are engineered to specific standards, in a process that ensures all MBU’s are produced to the same specifications. The benefit to the builder is that any two MBU’s can be connected vertically or horizontally, without the need to coordinate specific MBU’s.
Traditional building methods produce waste, in materials and in time spent to prepare the materials for assembly. LODESTAR MBU’s are manufactured under carefully managed processes, using the exact volume of required components, removing wasted materials from the process. When LODESTAR MBU’s are delivered to the construction site, they are installed with a reduced amount of labor, and without excess material, further reducing waste. Reducing building material waste and assembly time, further eliminates associated expense.
A common challenge on construction sites is secure storage and placement of supplies and related equipment, with consideration to the exposure to theft or being damaged. Builders can store the MBU’s offsite until they are ready to be installed, with the option to have delivery and installation coordinated to occur in sync with each task. The process of building with LODESTAR MBU’s reduces the demand for skilled labor which in turn reduces the need for space workers to occupy, space for construction equipment, and space for employee parking.
Unlike wood or steel, concrete does not burn, soften, or bend, concrete structures are more likely to remain standing through a fire. As the infrastructure of the building, fire-resistance enhances safety and security during the construction process and the finished product. The structure’s fire rating satisfies a higher level of fire code requirements, allowing for a more versatile use of the structure in more industry sectors.
A benefit of incorporating LODESTAR MBU’s into the construction process is that it reduces the amount and length of construction noise produced by traditional onsite construction, and once the structure is enclosed the noise is further reduced. Reducing the length and volume of noise pollution is essential when building in densely populated areas and in noise sensitive areas. Infill construction can be completed with a minimal disruption to surrounding residents, and with minimal disruption to local traffic, saving both time and money required to obtain permits and dealing with complaints.
LODESTAR MBU’s are built to meet or exceed strict building codes and standards, and the same architect-specified materials used in conventionally constructed buildings can be used in modular construction projects – wood, concrete, and steel.
When building in a factory, waste is eliminated by recycling materials, controlling inventory, and refined production procedures.
Because construction of modular buildings can occur simultaneously with the site and foundation work, projects can be completed 30% to 50% sooner than traditional construction.
LODESTAR MBU manufacturing is completed inside a factory, which mitigates the risk of weather delays. Modules are delivered on time, and can be installed immediately, creating a faster return on construction investment.
The indoor manufacturing environment reduces the risks of accidents and related liabilities for workers. The on-site modular assembly process further reduces risks associated with traditional framing and roofing techniques.
LODESTAR MBU’s can be stacked and connected to create a limitless selection of design options, while providing unique rooftop patios and greenspaces. LODESTAR MBU’s may be designed to take on external aesthetics of any existing traditional buildings, indistinguishable from traditionally counterparts.